Как я сделал тюноматик
Я всегда за то, чтобы купить нужную вещь, а не делать ее собственноручно. Штучное производство никогда не выдержит конкуренции с массовым. Даже мастеровые гитары совершенно бессмысленны, покуда они копируют серийные модели. Зачем же тогда делать свой бридж, если их на свете множество?..
Что не так с тюноматиками
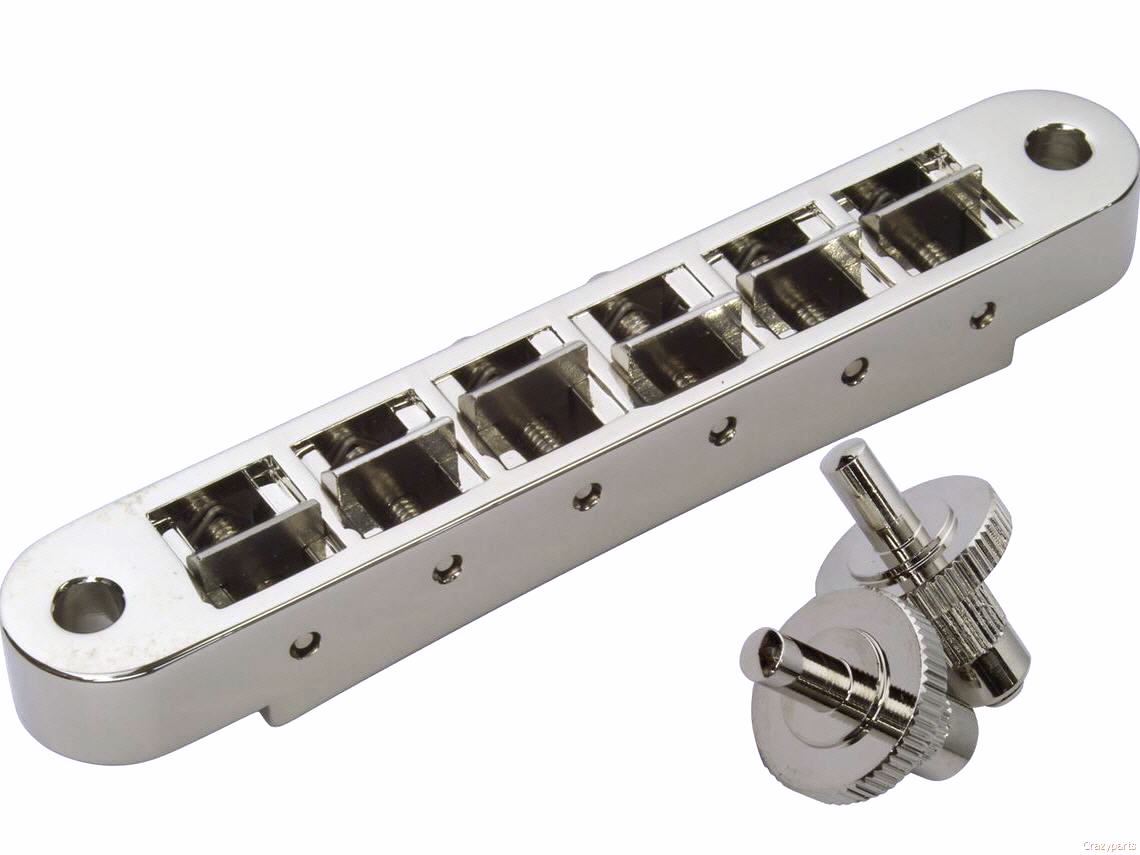
Тюноматики популярных фирм - Gotoh, Schaller, Hipshot, бесконечные азиаты, - мне не нравятся. Есть редкие исключения, типа Schaller STM; еще есть Callaham и ABM, у которых можно купить дорогущий бридж из стали или латуни. Но я-то говорю об обычном тюматике типа “нэшвилла” - и вот его, увы, сложно найти в том качестве, которое я считаю достойным.
Большинство тюноматиков делается из мягкого цинкового сплава, а то и вовсе из алюминия. Габарит бриджа почему-то никто не торопится увеличивать. Поэтому при чрезмерной нагрузке, которая на некоторых гитарах заложена в дизайн и неустранима, тюноматик прогибается:
Решение проблемы очевидно: возьми материал попрочнее или сделай стенки потолще… но всем, видимо, наплевать. Хотя так было не всегда - гибсон в семидесятых ставил классный Harmonica bridge, поди-ка согни его:
Увы, эта прекрасная штуковина осталась в прошлом. Как, впрочем, и другие удачные находки гибсона, типа жестяного экранирующего кожуха или более прочной головы :-)
Делать такие большие габариты совсем не обязательно. Вот бридж Yamaha SG восьмидесятых годов, мало отличающийся от “нэшвилла” по размерам:
С этим бриджем никогда ничего не происходит, он идеален. Не знаю, из чего он сделан (скорее всего, из латуни), но такая толщина боковых стенок сама по себе будет препятствовать деформации. Только вот найти этот бридж негде, не считая вторички. Настолько негде, что даже сама ямаха на современных японских SG ставит какой-то очередной клон ABR-1, который, мягко говоря, проигрывает родному ямаховскому бриджу сорокалетней давности. Ну, измельчал народ, что делать.
Таким образом, моя основная претензия - к стабильности корпуса типичного современного тюноматика.
Есть еще одна, мелкая: седла. Они обычно делаются из того же цинкового сплава, что и корпус. Цинк плохо подходит для удержания металлической струны, мягковат он. На многих немолодых инструментах с такими седлами, типа гибсонов 90-х годов, под струнами обнаруживаются глубокие протертые канавки, - иногда даже с заметными следами от обмотки. Естественно, это не способствует стабильности сетапа, а также увеличивает трение.
И еще эти седла нередко болтаются и противно резонируют на некоторых нотах. Даже вполне приличные готохи 103-й серии изредка зудят, а уж про ABR-1 - тот самый “винтаж с проволочкой”, - и говорить нечего.
Я бы, конечно, на все это наплевал: большинство тюноматиков работают приемлемо, особенно если не борзеть с углом перегиба (т.е. не опускать стопбар до пола) и по необходимости уплотнять посадку седел. Но ситуация не оставила выбора.
Тюноматик на акустике
Оказывается, на акустические гитары тюноматики тоже ставят. Вот Gibson J-45 Progressive:
Корни такой конструкции уходят далеко в прошлое. На Gibson Dove в шестидесятые годы попадался схожий бридж:
К сожалению, я не видел эту модель живьем, поэтому не могу сказать, все ли там было хорошо. А вот пресловутый J-45 - видел. Поэтому могу абсолютно уверенно заявить, что гибсон с этой моделью катастофически облажался. Собственно, ее уже и с производства сняли, хотя вышла на рынок она в 2015-м. Причина очень проста.

Тюноматик - высокий бридж. Именно поэтому на свете так мало фендер-подобных гитар с тюноматиками, а все гибсон-подобные инструменты обязательно имеют между грифом и корпусом некоторый угол.
В свою очередь, высота типичного акустического бриджа невелика. И увеличить ее нельзя: подставка будет трескаться, дека пучиться… То есть поставить на дредноут обычный тюноматик невозможно, нужен низкопрофильный.
Спрашивается, где достать низкопрофильный тюноматик для установки на акустику? Гибсон взял обычный бридж от леспола, из все того же цинкового сплава, и отпилил от него снизу порядка 3 мм. Осталось только натянуть сверху толстенные акустические струны - и катастрофа стала неминуемой.
Судя по всему, бридж на этой модели проваливается более-менее сразу. На форумах попадаются жалобы хозяев, посвященные этой проблеме. В этом нет ничего удивительного; напротив, удивительно, что кто-то вообще счел прочность этого бриджа достаточной!
Попытка выпрямления
Когда гитара (та самая J-45 progressive) попала в мастерскую, первое, что я попробовал сделать - разогнуть бридж обратно. Увы, как только пластичность понадобилась, ее не хватило: тюноматик треснул.
Я уже написал, что стараюсь обходиться покупными деталями. Поэтому я раздобыл какой-то обычный тюноматик нужного формата и сдал его на фрезеровку, чтобы получить аналог родного бриджа. Я планировал подложить под его центр твердый брусочек и таким образом защитить бридж от изгиба. Это тоже не сработало, и я не знаю в точности, почему - был в отпуске. “Обрезанный” цинковый тюноматик получается настолько слабым, что его ломает более-менее любая нагрузка. Даже с проставкой по центру на нем появилась трещинка.
Вот к чему мы пришли, потратив пару недель и шесть тысяч рублей на одни только запчасти:
Пошли отсюда, Илюша, ебал я такие разборки...
Замечу еще, что посадочное место в подставке этого гибсона предполагает использование определенного типа тюноматика - ABR-1. Это самая узкая модель. Расширять посадочное место под что-то более массивное очень не хотелось. Да и вряд ли простая замена на “нэшвилл” что-то дала бы: высоту-то ему все равно придется уменьшать… Еще сильнее сужает выбор готовых бриджей то, что межструнное расстояние на этой подставке больше, чем на бридже леспола, поэтому седла покупного бриджа должны быть без насечек по центру.
Что мне оставалось делать?..
Выбор материала
Где-то у Форда было прекрасное замечание: латунь занимает в металлообработке то же место, которое красное дерево занимает в столярке. И то и другое прекрасно обрабатывается, достаточно прочное, легко покупается, и к тому же отлично выглядит. По этой причине в мастерской валяется несколько латунных плит для выпиливания всяких деталек.
Вот, например, деталька для струнодержателя джазовой гитары:
А эта сделана для машинки Kahler:
Вот и этот бридж я решил делать из латуни. Правда, она со временем покрывается патиной, как памятник, а хромирование и прочую гальванику я пока не освоил - но не думаю, что это проблема. Вон, “алембик” делает свои бриджи из голой латуни и ничего, жутких денег стоит. Если припрет, можно раз в год при смене струн все располировывать.
Неожиданно важен состав сплава. Латунью называется сочетание меди и цинка в самых разных пропорциях. Для фрезеровки на станке, который ничего тверже алюминия обрабатывать не собирался, идеально подходит латунь с добавлением свинца. Свинец буквально в разы упрощает фрезеровку, обеспечивая мелкую хрупкую стружку, - поэтому такая латунь иногда называется “сыпучкой”. Самый популярный сплав такого типа - ЛС59-1, его легко купить, например, в prutki.ru.
Забегая вперед, добавлю, что главный враг фрезеровки металла - не твердость, а вязкость сплава. Мягкий металл, типа меди, буквально хватает фрезу и удивительно легко ее ломает.
Проектирование
С 2020-го я делаю абсолютно все CAD и CAM дела во “фьюжне”. О его преимуществах я уже писал (там же выложен большой ютуб-мануал по основам работы). Время от времени загадочный интерфейс и глюки заставляют понервничать, но в целом я очень доволен и вряд ли пересяду на что-то другое, даже если придется начать платить деньги.
Параметрическое моделирование, которым фьюжн славится, с непривычки сносит крышу - говорю это как бывший пользователь Rhinoceros3D. Но если разобраться, то окажется, что моделировать детальки под фрезеровку в нем очень удобно. Не говоря уж о возможности поправить размеры модели постфактум, это вообще что-то невероятное.
Я открыл фьюжн и нарисовал тюноматик с тремя парами седел.
Важные особенности:
Верх выпуклый, потому что это придает дополнительную прочность. Радиус, естественно, равен радиусу накладки. На современных тюноматиках тоже есть арка, но на нижней поверхности, а у нас там нет места.
Седла двигаются по мензуре вдоль струн, а не поперек корпуса тюноматика. Разница между одним и другим возникает из-за того, что тюноматик обычно ставится под углом, в том числе и на этом гибсоне. Этот угол очень мал, и никакой практической пользы из-за того, что я его учел, не предвидится. Однако глупо не использовать эту возможность, раз уж она есть.
Вместо отверстий по краям бриджа сделаны пазы - это особенность родного бриджа, которую я перенес без изменений. Опорные винты там тоже нестандартные, а резьбы - дюймовые. Легче всего было не трогать этот узел, что я и сделал.
Отверстие по центру бриджа нужно для того, чтобы сделать третью опору регулируемой. Большой вопрос, нужна ли вообще третья опора - все-таки новый тюноматик в разы прочнее родного. Но я решил перестраховаться.
В целом, дизайн получился похожим на Schaller STM:
Там же, во фьюжне, делается и программа для ЧПУ-фрезера.
Основная фрезеровка
Мой станок (Rosfrezer A09STM) расчитан на алюминий и древесину. Однако у него приличный запас по всем характеристикам, поэтому я спокойно обрабатываю на нем и материалы потверже, включая даже сталь.
Несколько важных моментов:
Пластиковый жертвенный стол, очевидно, не приемлем для обработки металла. Я просто кладу сверху лист фанеры, а уже на него - заготовку. Это не по правилам, но это хорошо работает.
Работать с металлом без СОЖ очень плохо, старайтесь этого избегать. Я использовал WD-40, потому что она под рукой, не сильно воняет и ее легко наносить прямо вручную. Это не идеальный вариант, но лучше так, чем вообще без жидкости.
Металлическая стружка и капли СОЖ покроют станок и особенно стол. Учитывая, что мы довольно часто кладем на стол свеженькие лакированные гитары, даже крохотный кусочек латуни может что-нибудь испортить. Также к столу перестал клеиться скотч - вд-40, очевидно, не способствует адгезии. Моя ошибка - в том, что я не застелил стол стретч-пленкой: это сильно помогло бы. Впрочем, латунная стружка может вернуться на стол, упав с элементов станка.
Расчет режимов фрезеровки я делал по таблице из каталога topincity.ru. Я полностью доверился этим людям во всем, что касается выбора оснастки для станка и сценариев ее применения, и это оказалось удачным решением. Важный момент: хотя у фрезы-кукурузы 4 ножа на боковой поверхности, на кончике у нее все равно обычно два. Поэтому я считал свои кукурузы двухзаходными.
Надень очки.
Поехали:
Вот что получилось после прохода фрезой 1/8":
Ща, пыль смахну…
Переходим на фрезу 1,5 и выгребаем ей уголки, а также добавляем небольшие углубления под края седел:
Теперь можно пройтись по периметру, снова фрезой 1/8". Почему бы ей еще в начале не пройтись? А потому что вырезанный из плиты бридж начнет болтаться, и это может осложнить дальнейшую фрезеровку. Поэтому сначала все внутренние дела, а периметр - в последнюю очередь.
Ну вот. Там миллиметр снизу остался:
Тут я допустил важную ошибку: не убрал латунь целиком внутри боковых пазов. Пришлось потом туда лазить пилками для верхних порожков :-) Но в целом довести периметр напильником было легко.
Во, уже можно любоваться, хотя все только начинается:
Следующий этап - седла.
Изготовление седел
Под рукой была плита 4 мм, а делать седлам толщину больше трех не хотелось. Можно было отпилить от четверки миллиметр на ленточке или просто сфрезеровать его, - но у меня нашлась прекрасная трехмиллиметровая пластина из бронзы, купленная на барахолке. Точный ее состав не известен, однако она капельку мягче моей латуни, красновато блестит, и вообще - что плохого? Вроде самое то.
Сломав три фрезы подряд с интервалом в пять минут, я изменил свое мнение. Это был тот самый случай вязкого подлого сплава, о котором я писал выше. Никаких ухищрения не помогли. К тому же я лишился последних фрез нужного размера (2 и 1,5 мм) - более крупные на седлах не сработали бы из-за необходимости иметь точные внутренние углы.
Я сдался, поставил в станок латунную плиту и прошелся по периметру седел фрезой 1/8". Во внутренние углы ей особо не залезешь (на фото они уже пройдены следующей фрезой):
А какая была “следующая фреза”, если я все подходящие поломал? Немного неловко писать: 0,7 мм. Такой фрезой делаются пазы под лады. Ничего другого под рукой не было, поэтому я с величайшей осторожностью начал подрезать внутренние контуры ей. И все получилось:
После полного провала с бронзой я совсем не ожидал, что эта авантюра завершится успехом. Более того, упомянутая фреза 0,7 в дальнейшем спокойно запилила еще несколько накладок, а затем погибла по моей глупости, когда я выставил не те обороты на шпинделе. В общем, люблю латунь-сыпучку.
Допилить седла было делом десяти минут.
Следующая процедура еще хитрее - нужно сделать отверстия под мензурные винты.
Боковые отверстия
Тут пришлось повозиться. Я сделал косую полочку под бридж и закрепил его шурупами и термоклеем:
Нулиться - т.е. показывать станку, где у него точка отсчета, - оказалось удобнее всего по отверстию для третьей опоры. Фреза 0,7 в данном случае используется лишь как тонкая палочка, позицию которой легко увидеть. Высота потом настраивается под другую фрезу.
Когда я выставил координаты, осталось поставить фрезу покрупнее и сделать углубления под шляпки винтов:
Затем - установить вместо фрезы сверло и пройти тюноматик насквозь шесть раз. Все, можно играться:
Третья опора
Отверстие по центру тюноматика диаметром 1,8 мм я досверлил до сквозного, а затем расширил сзади до 2,5 мм, не доходя до лицевой стороны:
После этого осталось только нарезать резьбу М3 и вставить установочный винтик. Смысл в том, что в наружное отверстие проходит только ключ, и оно выглядит изящнее, чем сквозная резьба М3.
Пост-обработка
Под этим термином скрывается долгое и скучное доведение всех поверхностей до блеска. Абсолютно ничем не отличается от шлифовки ладов или от изготовления латунного порожка: используется притир, мягкие абразивы и полировальная паста.
Примерный алгоритм: Р320, Р600, Ultrafine, абралон 2500, полировальная паста. Лицевую сторону лучше на плоском притире довести до Р1500 и полирнуть, чтобы не завалить углы. Вот что получается:
С седлами все примерно так же, а полировка вообще упрощена до предела:
Сборка и волшебные гаечки
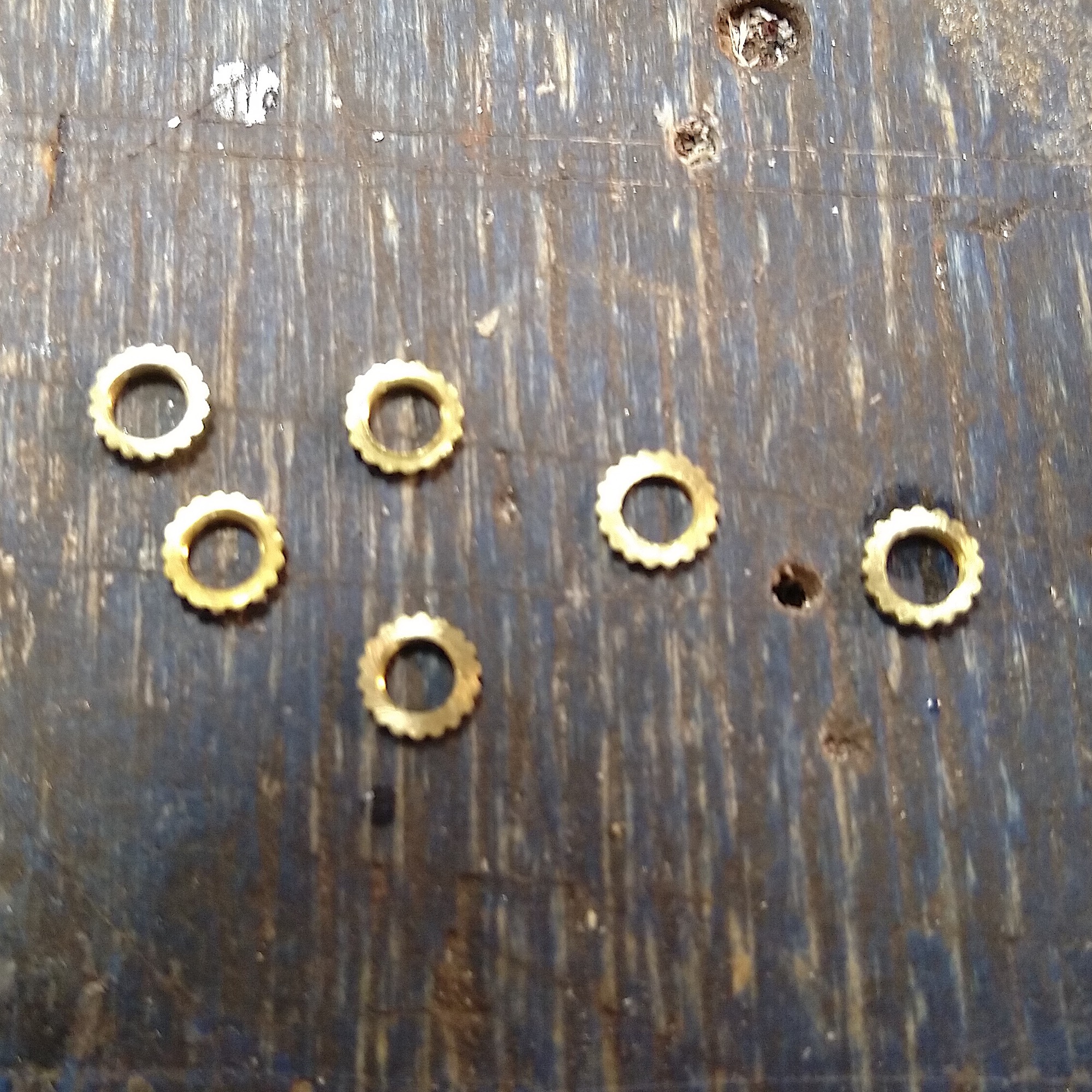
Для сборки тюноматика мне нужно было что-то, что не даст мензурным винтам вылезать из корпуса. Эта задача решается на серийных бриджах по-разному, но я решил просто зафиксировать винты тонкими гаечками, расположенными прямо внутри пазов под седла. Они чуток уменьшают диапазон регулировки мензуры, но это мелочь, а все остальное - сплошные плюсы. По сути это мало чем отличается от характерных проволочек на все том же “Нэшвилле”.
Другой вопрос - где взять красивые гаечки на М3? Я скажу: берется втулка под запрессовку, вот такая:
Сажаете ее на винт и спиливаете на гриндере. Ну, или на токарнике, если есть. Остается миллиметровая штука с юбочкой по краю.
Можно приступать к сборке:
Гаечка без проблем ловится узкогубцами и ими же удерживается, пока винт ее двигает на нужную позицию. Затягивать эту резьбу не следует, достаточно легкого касания. Естественно, чтобы гайка не раскручивалась, она сажается не просто так, а на тредлокер. Его излишки обязательно надо убрать любым растворителем. На фото я еще этого не сделал, поэтому виден красноватый налет на резьбе:
Результат
Готовый бридж:
А вот он на гитаре:
Под третью опору я вклеил небольшой металлический цилиндрик-таблетку.
Пришлось немного повозиться с подгонкой, но в результате все встало замечательно.
Виден важный нюанс: на этом тюноматике чудовищный угол перегиба. В общем-то он на многих акустиках такой - но это лишний раз показывает, насколько глупой была идея ставить сюда в качестве косточки подпиленный цинковый тюноматик.
При подгонке я все-таки сделал небольшие пропилы по центру седел, потому что мне хотелось чуть уменьшить высоту струн, а также избежать противного зудения струн (маловероятно, что оно при таком угле перегиба было бы, - но перестраховаться не вредно). Таким образом я добился идеальной регулировки высоты: диапазон начинается от 1 мм над 12-м ладом, а тюноматик настолько высокий, насколько возможно.
Мензура прекрасно отстроилась с большим запасом в обе стороны:
Да и выглядит все очень прилично:
Так-то вот.
Я очень доволен результатом. И рад, что теперь могу без всяких оговорок делать кастомные бриджи. Разве что токарки пока нет, поэтому безголовые - не ко мне. А вот если у вас какая-нибудь хитрая редкая гитара подвисла, и стандартное железо на нее не встает - буду рад помочь. Говорят, в паре километров от нас есть даже всякая гальваника на заказ, - клиент обращался, ему отлично все захромировали. Но этот вопрос мы оставим на следующий раз.
МТ17 апреля 2021